Success Story - Bark Residue Detection
March 22, 2022
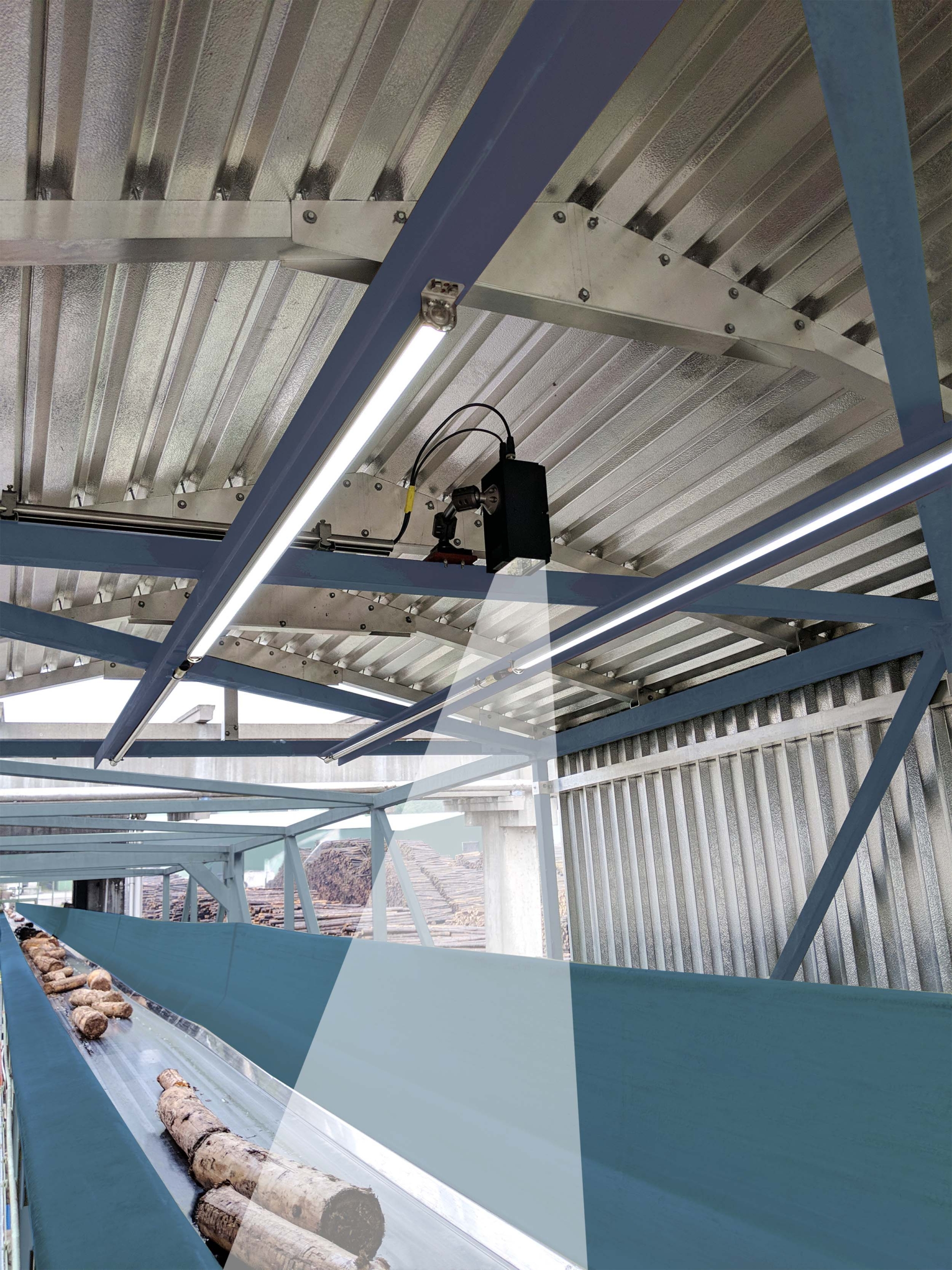
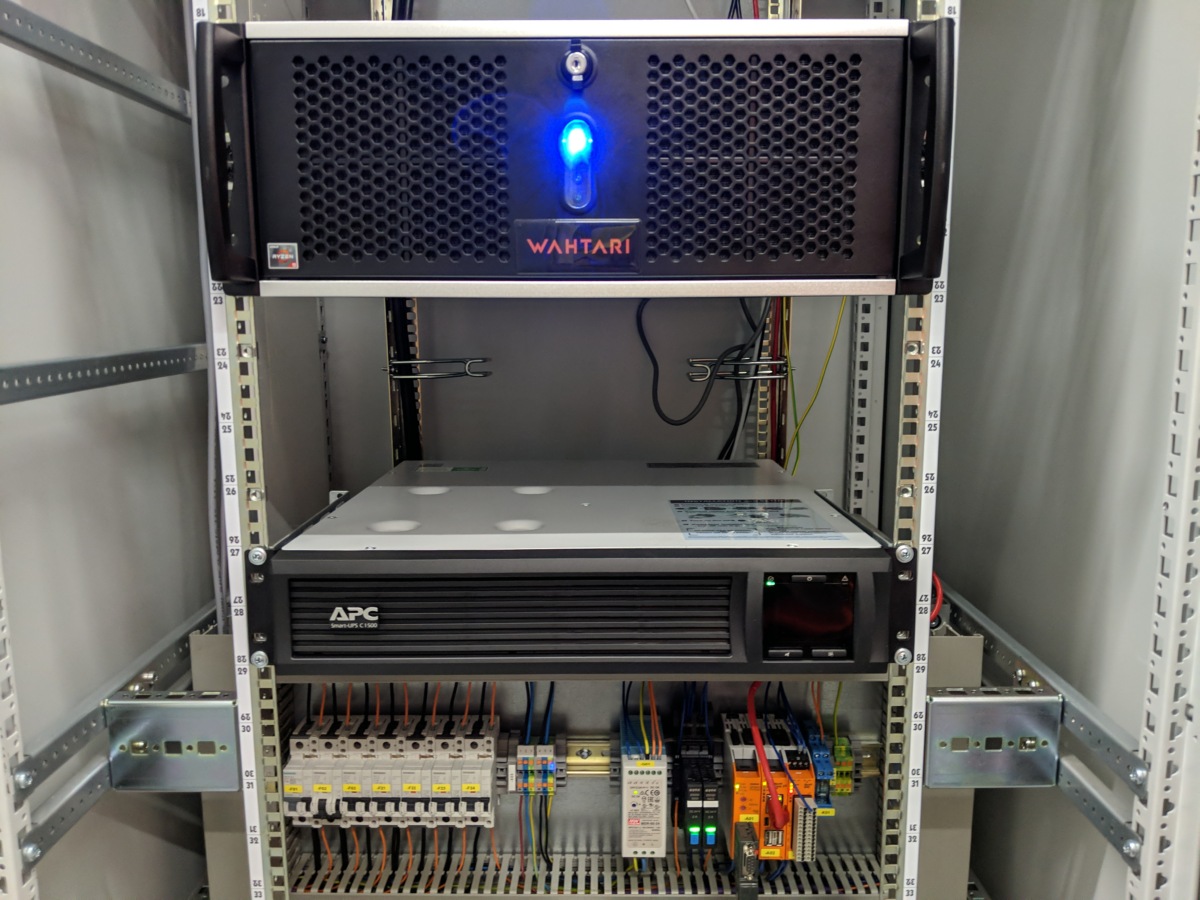
Problem and Challenges
At the production site, industrial wood (tree trunks) is prepared for subsequent processing into paper. Since the bark does not contain typical fiber material such as wood and therefore cannot be used for paper production, a large part of it is removed in a debarking drum (multi-trunk debarking). An optimal ratio of wood to bark (debarking degree) is important here: if too much bark is removed, material is wasted; if too much bark remains on the wood, the paper quality suffers.
Due to the process, however, the bark is not always optimally removed. Therefore, all debarked wood bats had to be subjected to a manual visual inspection and, if necessary, manually fed to a new debarking pass. Since this process is very labor-intensive, the manual inspection was to be automated. Wahtari faced the following challenges, among others:
the logs travel on a single-track conveyor belt and can lie singly, overlapping, in groups and touching each other
detection of contours, size and length of logs, wood piles and residual bark as well as the average value of all visible logs
display of the degree of debarking (= ratio of debarked and non-debarked wood) as a percentage value
adjustable threshold value for the degree of debarking as a basis for controlling an automatic sluice for recirculation
automatic inspection during operation (without belt stop), with variable belt speeds
special difficulty: detection of weather-related discoloration (weathering) and consideration of seasonal fluctuations (snow, rain on the wood)
The Solution
In order to replace the manual sorting, the customer has modified the conveyor belt and installed a controllable airlock. Human control was replaced by an AI-based, industrial camera system from Wahtari. This automatically detects the debarking quality and many other parameters and uses them to control the return airlock.
The automatic detection of the degree of debarking (and other parameters) is carried out by means of AI-supported image processing. The technology used is based on deep neural networks, which are trained project specifically for the detection of the residual bark content with image recordings of the processed logs.
The images for the training were taken on site during the process (in-line) by means of the installed Wahtari cameras. Subsequently, the AI was trained with image data of the sample strains provided. An evaluation of the still images initially showed a recognition accuracy of approx. 90%.
After installation, further images were taken during normal operation and the AI was trained again. Repeated training further improved the recognition rate. It was important to record the weathering of the different types of wood. Therefore, the system was trained several times over a period of 12 months. The final AI was calibrated with tens of thousands of selected images. Once the desired recognition rate was achieved, no further training was required.
The evaluation of the camera images takes place on a central computer system with central computer system that controls the airlock. After completing the training no internet connection is required for operation.
The Advantages
The AI-based camera system from Wahtari is a fully automated complete solution for optical inspection. Many times more powerful and precise than the human eye, the system inspects under industrial conditions, during operation and around the clock. It is easy to use, plug & play and allows convenient one-man operation.
The installed camera system consists of two project-specific industrial cameras and a computer system.
Optionally, the Wahtari nVision software can also be purchased. This offers an easy-to-use user interface for setting threshold values, process monitoring and documentation. Wahtari nVision is available for Linux and Windows operating systems and can be installed on in-house computers (e.g. laptops or tablets).
Operation via Wahtari nVision was not necessary for the customer. Instead, thanks to the numerous standard industrial interfaces (e.g. Profibus, Profinet, OPC/UA, Digital IO, etc.), the camera system could be easily and quickly integrated into the existing IT system. The system was controlled via the API, which could be made available via the industrial protocols (here: Profibus and OPC/UA).
The integration into the running operation is also simplified by standard cabling and power supply (220 V) of the Wahtari camera system. Due to the few and uncomplicated system components, the installation effort is minimal:
The industrial cameras with integrated mount and lighting are suspended at two different locations above the conveyor belt.
The computer system (embedded in a control cabinet, dimensions 50 cm x 60 cm x 40 cm (HxWxD)) is mounted on a wall during operation.
The system evaluates the images generated by the cameras and controls the return airlock via the industrial interfaces. This also means that neither an internet connection nor a cloud connection is required. This enables the highest data processing speeds and the lowest latencies. Since the customer data completely remains in the company, there is the greatest possible data security.
In the event of subsequent changes in the process (e.g. other tree types), the system can be adapted through quick and easy training.
Detection and Evaluation Performance
The cameras are suitable for indoor and outdoor use at temperatures between -20 and +50° Celsius. At belt speeds of up to 120 m/min, the system simultaneously records parameters such as debarking degree, belt speed, size, contours, length and diameter of logs and piles. Individual logs can be distinguished. Wood discoloration due to weathering is taken into account. The detection accuracy is over 98%, even in the event of disturbances such as dust, rain or snow. The inspection takes place in real time, the maximum inspection is approx. 150 milliseconds at 180 cm image diagonal. The degree of debarking quality and threshold values for the measurement can be set via Wahtari nVision. The sluice is controlled on the basis of the set debarking quality via the industrial interfaces of the computer system.